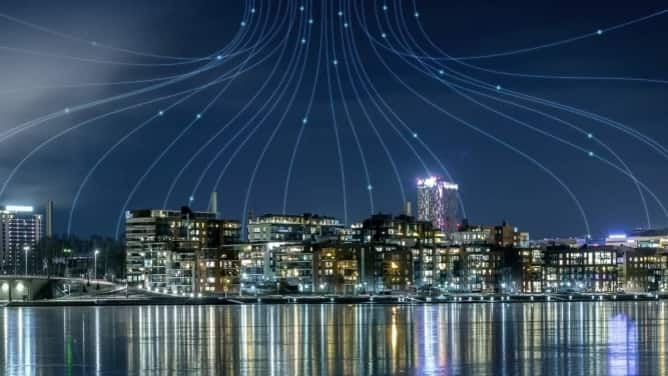
Connecting more than floors: a new era for elevators
Take a look at our full range of connected elevator solutions and find the one that’s right for your project.
Our job is to make your job easier. We make sure everything is in place for a smooth, trouble-free elevator installation process to keep your project on schedule and on budget, with no surprises.
Getting everything done on time and on budget relies on rock-solid preparation. Proper planning helps us make sure we can do our work as efficiently, safely, and cost-effectively as possible to keep your project on the fast track to success.
To make sure everything we need is in place before we begin installation, we can monitor and report the readiness state of the site. This involves checking the status of the following critical items:
Long before we arrive on site we use digital planning techniques like BIM to prepare for the installation process. This includes creating 3D digital models of elevators and escalators that contain information on things like building interface points, the forces applied to the building by KONE equipment, and even information about the materials we use. BIM also helps to make collaboration and communication easier between all parties during the project.
When you buy a solution from KONE, you’re getting far more than just equipment and installation. Every single project we handle is led by a dedicated, accredited project manager with solid experience of running similar projects.
Using our Installation Management Tool for mobile devices, anyone in your team who needs to can keep track of the installation process in real time and even communicate directly with the KONE project manager.
When it comes to installing your equipment, our goal is to keep everything tidy and efficient so that all personnel get their work done safely and on schedule. The KONE elevator installation process doesn’t require scaffolding, which cuts costs and minimizes disruption to other construction work on site.
Safety is our number one priority. All our installation technicians receive regular safety training and undergo safety audits to review their working practices.
Our installation process is also eco-efficient – we take care that all waste materials are properly sorted and recycled, and minimize the use of harmful substances like solvents.
Before your new elevator is handed over, we take every necessary measure to ensure that you’re taking delivery of a high-quality solution that will run as it should from day one. This includes testing the ride quality of every single elevator we install before we hand it over and providing you with a report detailing the results.
When it comes to maintaining your elevator in the long run, KONE DX Class elevators come with KONE 24/7 Connected Services built in, so we can use data gathered from your equipment to quickly identify and resolve any issues before they can cause a breakdown or service disruption.
Every project and every building is different, so there’s no one-size-fits-all approach to maintenance. When you choose KONE as your maintenance partner, you’ll benefit from a tailored maintenance plan for every single piece of equipment in your building.
You can also access performance, maintenance, breakdown, and repair data for your equipment using the KONE Online service portal.
Take a look at our full range of connected elevator solutions and find the one that’s right for your project.
Save time, cut costs, and boost productivity with our safe, reliable, and innovative construction time use (CTU) elevator and maintenance solutions.
Find out more about how KONE DX Class elevators add value for builders.